|
Dr. Benedek György: AEROJET 2
hőlégsugaras modellmotor
Ez
a modellmotor hosszas fejlesztő munka eredménye, mely viszonylag kis súly mellett nagy
tolóerőt ad. (Tolóereje önsúlyának kb. 7-szerese) Teljesítménye felülmúlja a
sorozatban gyártott, sokáig egyeduralkodó külföldi Dynajet Red Head motort. Ezen
hajtóművel 1955-től kezdve 6 éven keresztül mindig első helyet értem el országos
bajnokságokon, valamint minden más versenyen és 1957 októberben 281 km/ó sebességgel
abszolút sebességi világrekordot állítottam fel, melyet csak egy év múlva javított
meg a szovjet Ivannikov 301 km/ó-ra.

A 281 km/ó sebességet 0,3 mm-es két szál vezetőhuzallal és tiszta benzinnel értem
el. Egy szálas (monoline) vezetéssel, speciális üzemanyaggal, esetleg a hajtómű
továbbfejlesztésével a sebesség tovább növelhető.

A versenyeken előírt 2 szál 0,4 mm-es, 19,9 m sugarú acélhuzalon a gép átlagos
sebessége 250-255 km/ó volt, az eddigi legjobb versenyeredménye 265 km/ó.

A motorhoz legjobban bevált modell a Mazeppa III. modell, amelynek háromnézeti rajza a
“Repülés” c. folyóirat 1958 januári számában, valamint az MHS mod. oszt. 1958
és 1959 évi évkönyveiben jelent meg.

A hajtómű elkészítése nem jelent különösebb nehézséget, az alkatrészek
legtöbbje kis műszerész esztergapadon is elkészíthető. Az égéskamra és
kipufogócső viszont több darab lemezből készül, amelyeknek összeragasztásához
ponthegesztő gép szükséges.

Az 1. Jelű fej anyaga 1 mm-es lágy alumínium lemez, melyet fémnyomással kell a rajzon
látható formára hozni. A fej elkészítését leghelyesebb fémnyomó szakemberrel
végeztetni, de megfelelő fa-sablonok és nyomógörgő elkészítése esetén magunk is
hozzáfoghatunk.
A fémnyomás lépései a következők:
- 2 db külső forma nyomása.
- az egyik külső forma hosszméretre vágása és
homloklapjának kivágása,
- horonybenyomás
- a másik külső formából belső forma nyomása,
- a külső és belső forma összerakása, elől-hátul
pertlizés.
- szabályozás, az élek leesztergálása.
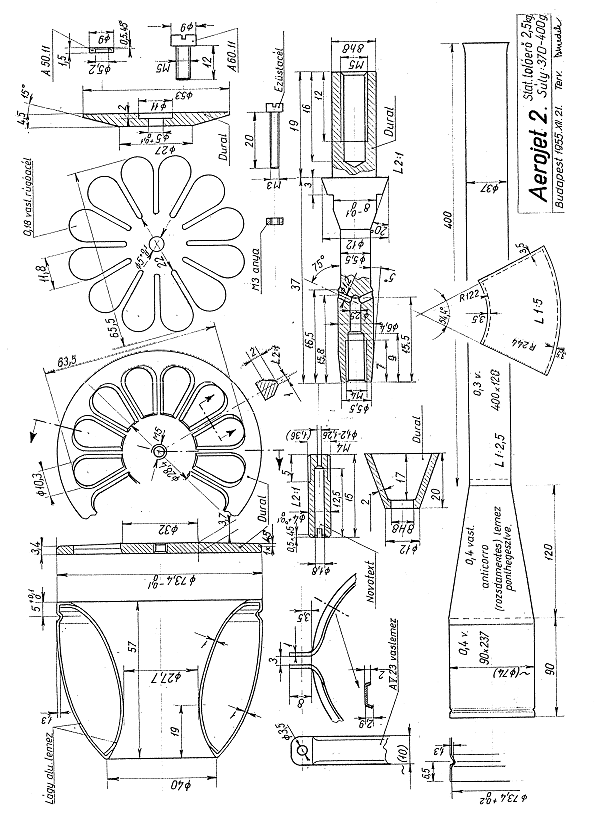 |
(A kép rákattintva nagyítható) |
Ezen műveletekhez egy külső forma-sablon, egy
osztható belső forma-sablon és egy horony sablon szükséges. Az első kettő fából,
míg az utóbbi fémből készülhet. A fej belső felének kontúrja pontosan megfelel a
rajznak.

A 2. Tűzfal anyaga durál lemez. Minél keményebb anyagot használunk, annál kevésbé
tudják a rezgő szeleplevelek a felfekvő felületet beverni, illetve megsérteni. A
tárcsa esztergálásánál a körte alakú átömlő nyílások pedig a pontos
kirajzolás után lombfűrészeléssel és reszeléssel hozhatók a rajzon látható
formára. A szelep felfekvő felülete enyhén kúpos. A felszorított szelep élei és a
tűzfal között így kb. 0,2 mm-es hézag marad, amely a könnyű indítás végett
szükséges.

A 3. számú szelep anyaga az eredeti motorban 0,18 mm-es rúgóacéllemez volt, de
0,18-0,20 mm között bármilyen más méret is megfelel. A szelep készítése kb. 1,5 mm
vastag gumikötésű csiszolótárcsával (gumikővel) történik. A szelep pontos
méretét papírra rajzoljuk, ezt apapírt az olajtalanított rugólemezre ragasztjuk és
a rajznak megfelelő formát gumikővel kicsiszoljuk.

Végezetül leoldjuk a papírt a papírt és lesorjázzuk az éleket.. A középső furat
lukasztó szerszámmal, ennek hiányában edzett acélból készített lyukasztóval
ólom,- vagy keményfa tuskón üthető ki. Kis gyakorlattal és ügyességgel 4-7 db.
szelep készíthető egyszerre.

A 4. számú pogácsa duralból készül. Szerepe a szelep kilengéseinek korlátozása
valamint a levelek rezgésszámának beállítása. Eszerint célszerű ebből az
alkatrészből több darabot készíteni, melyeknek síkméretét különféle átmérőre
esztergáljuk. Minél hosszabb a rezgő szeleplevél, annál alacsonyabb a rezgésszáma.
Aki szereti a kísérletezést, és kutató munkát, íves körvonalú pogácsával is
kísérletezhet. Az ívet legcélszerűbb körnek választani.

A tűzfal, szelep és pogácsa összeszorítását a 6. sz. csavar és az 5. sz. alátét
végzi el. A kilazulás elkerülésére nagyméretű csavarhúzót vagy pipa-csvarhúzót
használjunk.

A fej és tűzfal valamint az égéstér összeerősítésére szolgál a 7. sz. bilincs,
amely 1 mm-es lágy vaslemezből sablonra való kalapálással készíthető. A fej és az
égéstér hornyainak megfelelő élek esztergálással hozhatók pontos méretre.

A 8. sz. fúvóka az általános szokásoktól eltérően műanyagból, textilbakelitből
készül. Ez igen fontos a hőszigetelés végett, mert a fémből készült, erősen
átmelegedett fúvóka a műanyag-benzinvezetéket megolvaszthatja.. A fúvóka
furatmérete szabályozza az üzemanyag-adagolást. Ennek összhangban kell lenni a
rezgésszámmal, valamint a tank helyzetével is. Általában 1,2-1,25 mm a furatméret,
de némi kísérletezés után ezt bővebbre vettem (1,36 mm.) és a benzin adagolást a
tartály kivezető csövébe helyezett fojtó csavarral állítottam be. Ez lényegesen
kényelmesebb szabályozást tesz lehetővé, mint a régebben szokásos fúvóka csere.

A 9. sz. porlasztó anyaga is durál. Ha két porlasztófuratot használunk, úgy 1,2
mm-es furat alkalmazandó. Valamivel jobb teljesítmény és egyenletesebb
üzemanyag-adagolás érhető el szabályosan elhelyezett 6 db. 0,8 mm-es
porlasztófurattal.

Az egyszerűbb gyártás végett a porlasztó 10. sz. terelőkúpját külön darabból
készítjük, melynek anyaga ugyancsak durál. A porlasztót és terelő kúpot a
tűzfalból (2 sz.) kiálló M5-ös csavar végére csavarjuk és a meghúzás végett a
porlasztóra 8 mm-es kulcsnyílást reszelünk.

A 11. sz. cső (égéstér, kúpos átmeneti rész és kipufogócső) rozsdamentes
acéllemezből készül. Ennek vastagsága 0,3-0,4 mm-es lehet. A vékony lemezből
könnyebb, a vastagabból nehezebb, de tartósabb cső készíthető. Az eredeti
hajtóműnél igen jól bevált az a megoldás, amelynél a hőnek kitett égéstér és
az átmeneti kúp 0,4, a kipufogócső viszont 0,3 mm-es lemezből készült. A megadott
méreteknél vékonyabb vagy vastagabb lemez nem ajánlható a sérülékenység illetve
ellenkező esetben a nagy önsúly miatt.

Rozsdamentes acél hiányában a kipufogócső 0,4-0,5 mm-es vaslemezből is
készíthető, ennek élettartama azonban lényegesen kisebb lesz, hamarabb elég. A cső
élettartama krómozással, illetve nikkelezéssel növelhető, ekkor ugyanis a levegővel
érintkező külső fal nem oxidálódik.

A lemezek pontos mérete a rajzon számokkal van megadva, az átmeneti kúpnak pedig a
kiterített mérete meg van rajzolva. A méretekben az átlapolások is benne
foglaltatnak. A lemezeket fa vagy fém sablonokon kalapáljuk fa kalapáccsal hengeres
illetve kúpos méretre. A ponthegesztést a kipufogócsővel kezdjük, melyet két
oldalról hegesztünk. Utána a kúpos, majd a hengeres égéstér hosszanti hegesztése
következik. A hegesztési pontok sűrűn egymás mellett legyenek. Ezután a találkozó
éleket kalapáccsal sablonon egymáshoz illesztjük.

A következő lépés a kúpos és kipufogócső hegesztése, végezetül pedig az
égéstér és a kúpos cső hegesztése. Ha ilyen sorrendben végezzük el a hegesztést,
a hegesztőgép elektródájának csak 21 cm-re kell kiállnia. Az egyes alkatrészek
hegesztésénél vigyázzunk, hogy a csövek geometriai tengelyei közösek legyenek. Az
égéstér első éleit szükség esetén síkra dolgozzuk majd belenyomjuk a hornyot. A
kipufogócső hátsó, trombitás része vasrúdon, vaskalapáccsal tágítható ki.

A 7. sz. bilincs megszorítására szolgál a 12. Anya és a 13. Csavar. Itt közönséges
hengerelt csavar nem ajánlható, mert a menetek hamar tönkremennek. A 7. sz. a füleknek
teljes szorítás esetén sem szabad összeérni, kell lenni hogy legalább 1 mm hézag
maradjon. |
|
|
|